The efficiency of a simple transformer construction can be improved by bringing the two windings within close contact with each other thereby improving the magnetic coupling. Increasing and concentrating the magnetic circuit around the coils may improve the magnetic coupling between the two windings, but it also has the effect of increasing the magnetic losses of the transformer core.
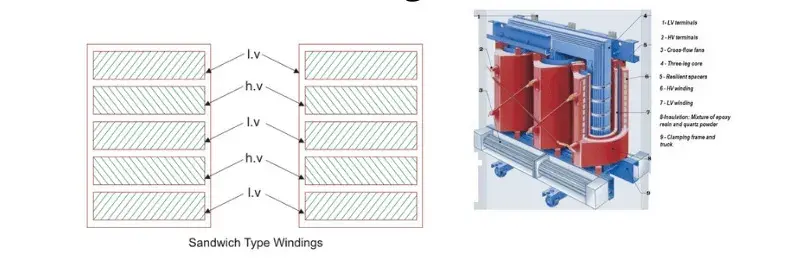
As well as providing a low reluctance path for the magnetic field, the core is designed to prevent circulating electric currents within the iron core itself. Circulating currents, called “eddy currents”, cause heating and energy losses within the core decreasing the transformer’s efficiency.
These losses are due mainly to voltages induced in the iron circuit, which is constantly being subjected to the alternating magnetic fields setup by the external sinusoidal supply voltage. One way to reduce these unwanted power losses is to construct the transformer core from thin steel laminations.
In most types of transformer construction, the central iron core is constructed from of a highly permeable material commonly made from thin silicon steel laminations. These thin laminations are assembled together to provide the required magnetic path with the minimum of magnetic losses. The resistivity of the steel sheet itself is high, thus reducing any eddy current loss by making the laminations very thin.
These steel transformer laminations vary in thickness’s from between 0.25mm to 0.5mm and as steel is a conductor, the laminations and any fixing studs, rivets or bolts are electrically insulated from each other by a very thin coating of insulating varnish or by the use of an oxide layer on the surface.
Transformer Winding Arrangements
Transformer windings form another important part of a transformer construction, because they are the main current-carrying conductors wound around the laminated sections of the core. In a single-phase two winding transformer, two windings would be present as shown. The one which is connected to the voltage source and creates the magnetic flux called the primary winding, and the second winding called the secondary in which a voltage is induced as a result of mutual induction.
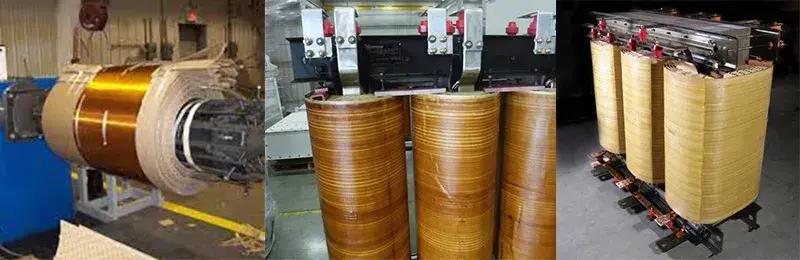
If the secondary output voltage is less than that of the primary input voltage the transformer is known as a “Step-down Transformer”. If the secondary output voltage is greater than the primary input voltage it is called a “Step-up Transformer”.
types of core
Core-type Construction
The type of wire used as the main current carrying conductor in a transformer winding is either copper or aluminium. While aluminium wire is lighter and generally less expensive than copper wire, a larger cross sectional area of conductor must be used to carry the same amount of current as with copper so it is used mainly in larger power transformer applications.
Small kVA power and voltage transformers used in low voltage electrical and electronic circuits tend to use copper conductors as these have a higher mechanical strength and smaller conductor size than equivalent aluminium types. The downside is that when complete with their core, these transformers can be much heavier.
Transformer windings and coils can be broadly classified in to concentric coils and sandwiched coils. In core-type transformer construction, the windings are usually arranged concentrically around the core limb as shown above with the higher voltage primary winding being wound over the lower voltage secondary winding.
Sandwiched or “pancake” coils consist of flat conductors wound in a spiral form and are so named due to the arrangement of conductors into discs. Alternate discs are made to spiral from outside towards the centre in an interleaved arrangement with individual coils being stacked together and separated by insulating materials such as paper of plastic sheet. Sandwich coils and windings are more common with shell type core construction.
Helical Windings also known as screw windings are another very common cylindrical coil arrangement used in low voltage high current transformer applications. The windings are made up of large cross sectional rectangular conductors wound on its side with the insulated strands wound in parallel continuously along the length of the cylinder, with suitable spacers inserted between adjacent turns or discs to minimize circulating currents between the parallel strands. The coil progresses outwards as a helix resembling that of a corkscrew.
magnetic core
Transformer Core
The insulation used to prevent the conductors shorting together in a transformer is usually a thin layer of varnish or enamel in an air cooled transformer. This thin varnish or enamel paint is painted onto the wire before it is wound around the core.
In larger power and distribution type transformer’s, the conductors are insulated from each other using oil impregnated paper or cloth. The whole core and windings is immersed and sealed in a protective tank containing transformer oil. The transformer oil acts as an insulator and also as a coolant.